Anodizing: Types and Benefits
- Sam Awad
- Jul 31, 2023
- 6 min read
Introduction
Anodizing is a chemical process that involves the electrochemical conversion of a metal surface, primarily aluminum, into a durable and corrosion-resistant oxide layer. This process not only enhances the aesthetic appearance of the material but also provides numerous protective benefits. Let's delve deeper into the world of anodizing and explore its types and benefits.
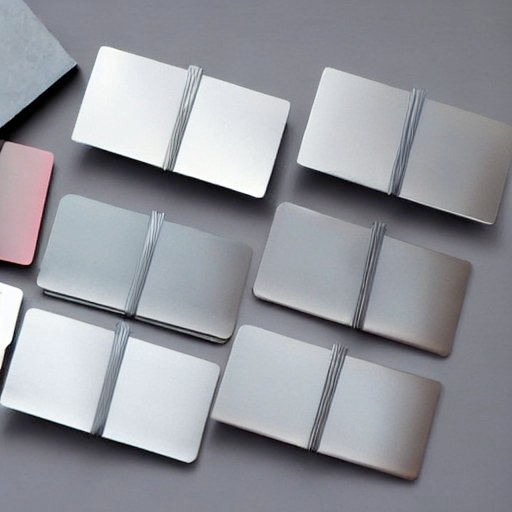
Definition of Anodizing
Anodizing is a surface treatment technique that involves the controlled oxidation of an aluminum surface to form a layer of aluminum oxide. This oxide layer possesses exceptional properties, such as corrosion resistance, hardness, and electrical insulation, which make it highly desirable for various applications.
Importance of Anodizing
Anodizing plays a crucial role in enhancing the performance and lifespan of metals, particularly aluminum. By creating a protective oxide layer, anodizing significantly improves the material's resistance to corrosion, wear, and environmental factors. It also offers an opportunity to add vibrant colors and patterns to the surface, making it visually appealing.
Historical Background of Anodizing
The history of anodizing dates back to the early 1920s when this process was first commercialized for aluminum applications. Originally utilized for military purposes, anodizing gradually gained popularity across different industries due to its outstanding protective properties and decorative potential. Today, it has become a standard procedure in countless manufacturing processes.

How Anodizing Works
To better understand anodizing, it is essential to comprehend the electrochemical process and the interaction between the anode and cathode during the treatment, leading to the formation of the oxide layer.
Electrochemical Process
Anodizing is primarily an electrochemical reaction that occurs when aluminum, serving as the anode, is immersed in an acidic electrolyte bath. A direct current is then passed through the bath, creating a controlled oxidation process on the metal's surface. This oxidation process converts the aluminum into an aluminum oxide layer.
Anode and Cathode Interaction
During anodizing, the metal piece being treated acts as the anode, while a separate cathode is also present in the electrolyte bath. The cathode facilitates the flow of electrons necessary for the electrochemical reaction to take place effectively. This interaction ensures a consistent and uniform coating of the oxide layer across the surface of the material.
Formation of Oxide Layer
As the anodizing process progresses, the aluminum surface oxidizes, resulting in the growth of a dense and adherent aluminum oxide layer. This layer provides exceptional protection against corrosion, wear, and external environmental factors, making the material significantly more durable and long-lasting.
Benefits of Anodizing
Anodizing offers a wide range of benefits that make it the preferred surface treatment technique for various industries. Let's explore the advantages it provides:
Corrosion Protection
One of the most significant benefits of anodizing is its exceptional corrosion resistance. The oxide layer formed during the anodizing process acts as a barrier, preventing direct contact between the metal and corrosive agents. This shielding effect enhances the material's longevity, especially in harsh environments exposed to moisture, chemicals, or saltwater.
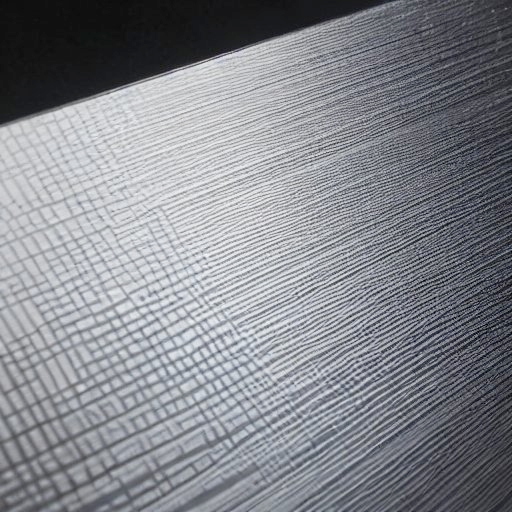
Durability and Wear Resistance
The oxide layer created through anodizing significantly enhances the material's hardness and wear resistance. This makes anodized surfaces less prone to scratches, abrasion, and general wear and tear. Therefore, anodized components are ideal for applications where durability and long-term performance are critical.
Enhanced Aesthetic Appearance
Aside from its protective benefits, anodizing allows for the customization of the material's appearance through a wide range of colors and finishes. By utilizing various dyeing techniques, anodized aluminum surfaces can achieve vibrant and consistent colors, making them visually appealing for architectural, decorative, and branding purposes.
Types of Materials Suitable for Anodizing
While anodizing is commonly associated with aluminum, it can be applied to several other metals and alloys. Let's take a closer look at the different materials suitable for anodizing:
Commonly Anodized Materials
Apart from aluminum, other common materials suitable for anodizing include titanium, magnesium, and zinc. These metals possess similar anodization characteristics, allowing for the formation of protective oxide layers that enhance their performance.
Aluminum - The Most Commonly Anodized Material
Among all the materials suitable for anodizing, aluminum takes the lead. Its widespread use in various industries, coupled with its exceptional anodizing properties, has made it the primary choice for anodization processes. Aluminum offers excellent adhesion for the oxide layer and allows for a wide range of colors, making it highly versatile for different applications.
Other Metals Suitable for Anodizing
While aluminum dominates the anodizing industry, certain alloys and metals like titanium, magnesium, and zinc can also be anodized. However, the anodizing process for these materials may require specific adjustments to achieve optimum results.
Anodizing Colors and Dyeing Process
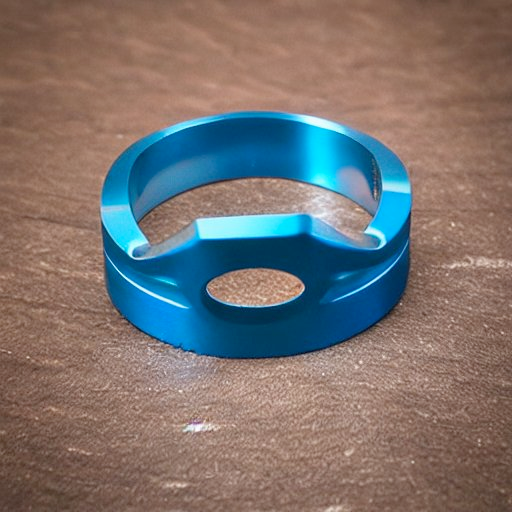
Wide Range of Color Options
Anodizing offers an extensive palette of colors to choose from when enhancing the appearance of metal surfaces. From vibrant reds to elegant blues or even metallic shades, anodized materials can be customized to match the desired aesthetic and design requirements.
Common Anodizing Colors
While the choice of colors is virtually limitless, some popular anodizing colors include black, bronze, gold, and silver. These colors can be achieved through the use of specific dyes or by utilizing natural processes that alter the thickness of the oxide layer, resulting in varied light absorption and reflection.
Dyeing Techniques for Aluminum
The dyeing process for anodized aluminum involves immersing the material in an electrolyte solution containing organic or inorganic dyes. By applying an electric current, the dye molecules are attracted to the porous structure of the oxide layer, penetrating it and resulting in a permanent and vibrant coloration.
Step-by-Step Anodizing Process for Aluminum
Pre-Treatment: Cleaning and Finishing
Before anodizing, the aluminum surface undergoes a rigorous cleaning process to remove any impurities or contaminants. This preparation stage ensures optimal adhesion of the oxide layer and promotes a uniform finish. Finishing techniques such as polishing or sanding may also be employed to achieve the desired surface texture.
Anodizing: Using Chromic Acid or Sulfuric Acid
Once the pre-treatment is complete, the aluminum piece is immersed in an electrolyte bath. The anodizing process can be carried out using either chromic acid or sulfuric acid as the electrolyte solution. Chromic acid anodizing typically produces a thinner and more transparent oxide layer, while sulfuric acid anodizing results in a thicker and more robust layer.
Coloring: Dyeing Anodized Aluminum
After the anodizing phase, the anodized aluminum can be subjected to the dyeing process to introduce a desired color. The material is immersed in a dye solution, and an electric current is passed through it, allowing the dye to penetrate the porous oxide layer and achieve vibrant and long-lasting colors.
Sealing: Preventing Corrosion and Surface Damage
To further enhance the protective characteristics of anodized aluminum, a sealing step is employed. This involves closing the pores of the oxide layer, preventing contaminants from entering and improving corrosion resistance. Sealing can be achieved through various methods, such as hot water sealing or the use of specialized sealing solutions.
Types of Anodizing
Type I - Chromic Acid Anodize
Chromic acid anodize, also known as Type I anodizing, produces a thin and dense oxide layer on the aluminum surface. The resulting coating offers excellent corrosion resistance and is often used as a base for subsequent coatings or as an electrical insulator in electronic applications.
Type II - Sulfuric Acid Anodize
Type II anodizing, utilizing sulfuric acid as the electrolyte, creates a thicker and more durable aluminum oxide layer compared to chromic acid anodize. This type of anodizing is commonly used for architectural and decorative applications, providing both enhanced corrosion resistance and vibrant coloring options.
Type III - Hard Anodize or Hard Coat
Hard anodize, or Type III anodizing, involves an electrolytic process that generates an exceptionally thick and hard oxide layer on the aluminum surface. This type of anodizing is renowned for its exceptional wear resistance and is often utilized in applications requiring high-strength materials, such as aerospace or military equipment.
Other Less Common Anodizing Methods
Apart from the three main types mentioned above, there are other specialized anodizing techniques available. These include sulfuric acid hard anodizing, phosphoric acid anodizing, and boric-sulfuric acid anodizing, each offering unique properties to meet specific application requirements.

Advantages and Disadvantages of Anodizing
Benefits of Anodizing
Exceptional corrosion resistance |
Enhanced wear resistance and durability |
Aesthetic appeal with a wide range of colors and finishes |
Excellent electrical insulation properties |
Environmentally friendly process |
Provides added surface hardness |
Limitations of Anodizing
Limited application to specific metals, primarily aluminum and certain alloys |
In some cases, anodized surfaces may be prone to water staining |
Surface defects or imperfections on the base metal may be accentuated after anodizing |
Conclusion
Recap of the Importance of Anodizing
Anodizing is a highly significant surface treatment technique that offers a multitude of benefits, including corrosion protection, increased durability, and enhanced aesthetic appearance. By forming a robust oxide layer on metal surfaces, anodizing significantly improves their performance and extends their lifespan.
Future Developments in Anodizing Technology
As technology advances, it is likely that we will witness further developments in anodizing techniques and materials. Innovations may include improved dyeing processes, novel electrolytes, or modifications to anodizing equipment, ultimately enhancing the overall efficiency and customization capabilities of the process.
Final Thoughts on Anodizing as a Chemical Process
Anodizing represents a versatile and effective method for enhancing the properties of metals, elevating their performance, and adding a touch of visual appeal. Whether it is for architectural purposes, industrial applications, or creative endeavors, anodizing continues to play a vital role in numerous industries, contributing to the longevity and reliability of countless products and structures.
Zero Machining offers a wide range of anodizing services for your products, contact our team today to learn more about our capabilities to meet your product requirements.
Kommentare